Though machines have been used to mould iron into utensils and spare parts for some time now, some blacksmiths still do this work by hand.
In a small corner of Rawalpindi along Leh Nullah and near the main Spare Parts Market, there are many factories where old iron utensils and spare parts are melted and moulded into new parts.
Such workshops generate employment for many workers where they work with hot metal in the hot weather. Workers start their day at dawn and work till the evening with small breaks for lunch and tea.
Every two hours that they spend by the hot ovens, they get showers to cool their bodies down where they also get to talk to one another and discuss their problems.
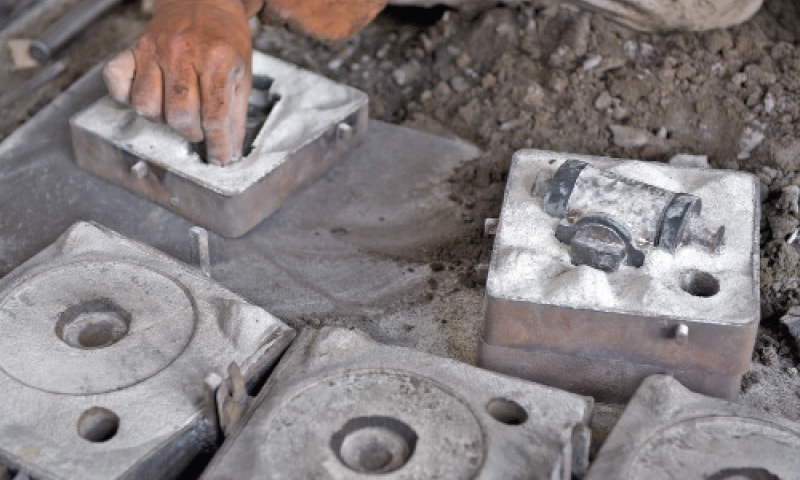
The process of making spare parts in local workshops involves three or four steps from melting the iron and turning it into spare parts and the process requires more than three workers and calls for the work of scrap collectors, blacksmiths and labourers.
These workshops collect scraps from different sources which is then melted in burners fuelled by furnace oil. Special buckets made of metals other than iron are filled with pieces of iron scrap and put in the burner for an hour.
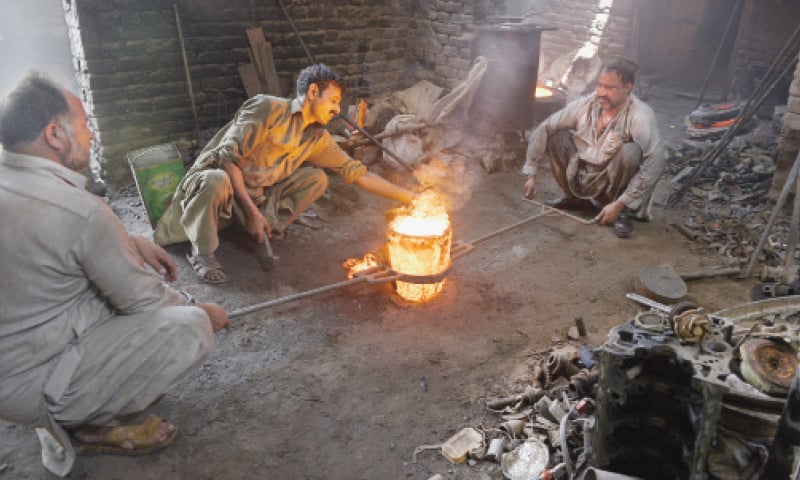
In the meantime, three workers prepare a moulder with sugar juice and crush. When the iron turns red hot, two workers bring out the bucket and pour the red liquid into the moulder for spare parts.
Two more workers then open the moulders and leave the new spare part in the open to cool down. It takes two days to make spare parts weighing between 60 and 80kg.
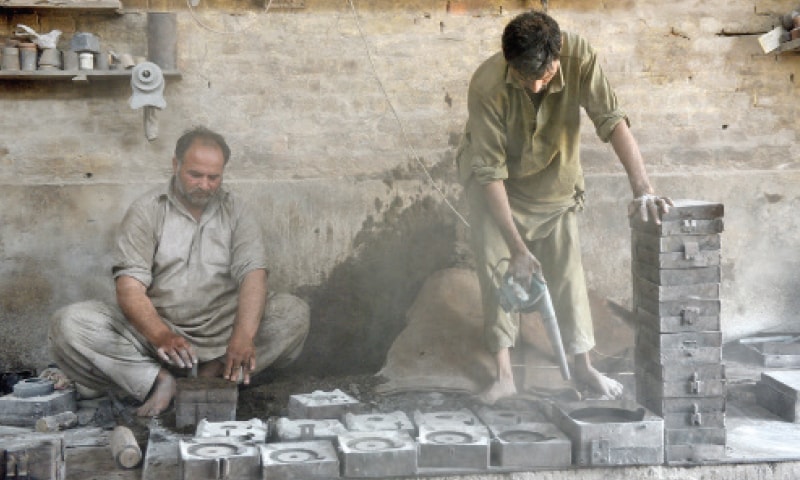
The new spare part is then taken to be polished and packed.
Abdul Sattar, the owner of one such workshop said a sample of the spare part is provided by the dealer and that he makes spare parts for vehicles, kitchen appliances and other machines used for domestic and commercial purposes.
He said his workshop does not have gadgets for monitoring the temperature in the burner and that the process is carried out with the experience of the blacksmiths and workers who know when the oven is ready to put the iron scrap in.
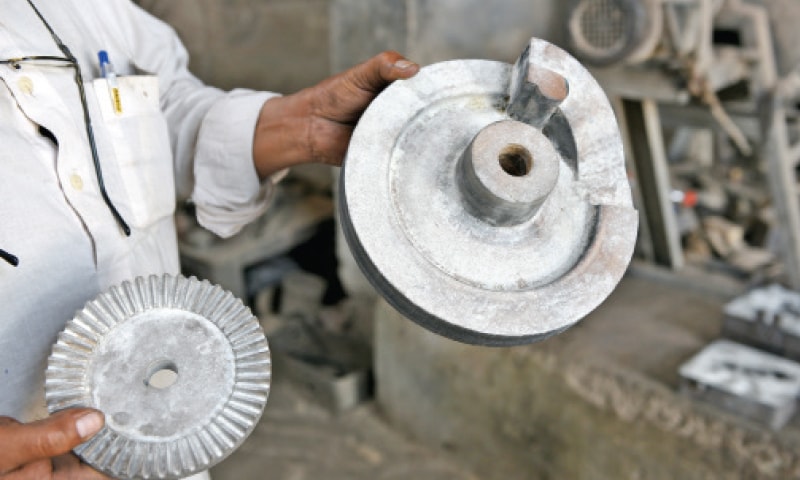
He said sugarcane waste is bought to fill in the mould and that all waste is recycled to make new spare parts. He said shopkeepers sell these spare parts with a two-year warranty and that they are sold at a price less than what company spare parts are sold for as company spare parts are not made from recycled iron.
He said some of the iron is wasted when cleaning liquid iron with salt.
“A dirty foam rises to the top when salt is put in liquid iron which has to be removed,” he said.
Published in Dawn, May 28th, 2017