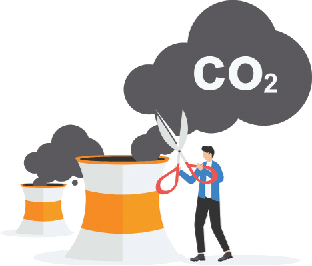
Decarbonisation — reducing ‘carbon intensity’ or lowering the amount of greenhouse gas emissions produced by burning fossil fuels — of the country’s cement industry has never been more important as the global cement and concrete industry has established new targets to slash and even eliminate emissions.
The Global Cement and Concrete Association (GCCA) targets a 20 per cent reduction of carbon dioxide per ton of cement and a 25pc reduction of CO2 per cubic meter of concrete by 2030 compared to the 2020 levels. The GCCA also calls for complete decarbonisation by 2050 to ‘achieve the net zero emissions target agreed by nations to slow down global warming’.
This means Pakistan’s cement industry, which accounts for about 7-8pc of the total national greenhouse gas emissions — equal to the global industry average- must actively reduce its carbon footprint in line with the industry and global targets of a net-zero future.
But cement, central to our modern way of life, is particularly hard to decarbonise as it requires novel solutions and materials for a transition to a decarbonised future, as well as huge massive investments in new technologies, research and development of innovative raw materials and cleaner energy options to ditch dirty fossil fuels.
The industry’s emissions have surged by 687pc in 2020 relative to 1990
A recent study — Decarbonising Cement Production in Pakistan — conducted by the National University of Sciences & Technology (Nust) and Policy Research Institute for Equitable Development, analyses the domestic cement sector dynamics, lays out a strategic roadmap for its decarbonisation journey, and maps out the scale of direct and indirect carbon emissions from cement production as well as available technologies and alternate fuels that can help the industry in its transition to a ‘low-carbon cement production’.
The study argues that “substantive emission reductions are feasible at a low cost through clinker (which accounts for 90pc of emissions in cement production process, making it a high priority for industry players to address) substitution and energy efficiency measures” despite the challenges to decarbonisation of the industry.
The report points out that cement industry emissions have surged by 687pc in 2020 relative to 1990. In 1990, the Pakistan cement industry contributed around 2.7 million tons of CO2 emissions from fuel combustion, which have shot up to approximately 21m tons.
The study projects an emissions growth trajectory in the forthcoming decades. In 2030, a projected increase of 172pc indicates an intensified environmental impact because of industrial expansion, while in 2040, the projection escalates to 240pc, reflecting the consequences of unabated growth trends.
Furthermore, the year 2050 culminates in a projected 308pc increase in greenhouse gas (GHG) emissions, underlining the urgency of adopting transformative practices to address the cumulative impact of industrial expansion. At present, Pakistan’s cement industry has an annual clinker production capacity of 78m tons and cement manufacturing capacity of 86m tons, or less than 1pc of the global capacity of 4.2 billion tons.
By 2030, Pakistan’s share in global capacity is expected to rise to 2pc. An industry source says the rule of thumb is that each ton of cement produced emits 0.9 tons of carbon emissions into the atmosphere, emphasising the need for action to shift to technologies, raw materials, and fuels that can help transition to low-carbon cement production processes.
Challenges
Dr Mohammed Faheem Khokhar, a Nust professor and researcher, says the major challenges to the cement industry’s transition to a low-carbon future include its coal dependency on the calcination process that removes carbon from limestone (calcium carbonate) through combustion to yield clinker, lack of regulatory framework and policy support to the industry for decarbonisation, high transition costs, and absence of any incentives available for the transition.
He proposes a multi-pronged approach involving technological upgradation, regulatory reforms, incentives, international collaboration, and cross-sector collaboration to facilitate the industry’s shift to alternative fuels, renewable energy, clinker substitution, energy efficiency and carbon capture technologies for achieving the goal of decarbonisation in Pakistan’s cement industry.
The cement industry faces two seemingly divergent challenges: Pakistan’s per capita cement consumption, at 182kg, falls short of the global average of 550kg, indicating an untapped market potential. Its heavy reliance on coal, accounting for nearly two-thirds of its energy consumption, exposes it to the fluctuations of global coal prices. If local demand for cement is encouraged to increase, it is bound to have deleterious impacts on the environment and the climate.
“By transitioning to sustainable practices, Pakistan can drive its cement sector to be globally competitive while spearheading climate change mitigation,” Professor Khokhar maintains. “The pressing need to reduce this industry’s carbon footprint and a pivot towards its simultaneous growth and sustainability is self-evident.
“This shift is not just an environmental imperative; it is also necessary to enhance the industry’s resilience and global competitiveness. Reforming the energy usage practices of cement plants will not only reduce their environmentally toxic emissions but will also be able to keep their energy costs lower. This, in turn, will help it expand domestic consumption of cement without endangering the environment and compete with other cement manufacturers in the international market.”
Pakistan has witnessed a steady rise in greenhouse gas emissions in recent decades. Since 1990, the country’s GHG emissions have surged by over 160pc — a figure below the 175pc average increase among the Middle East, North Africa, Afghanistan, and Pakistan nations but substantially exceeding the global average of 50pc. This stark contrast underscores the imperative for Pakistan to adopt effective carbon mitigation strategies to curb its escalating emission levels.
According to Professor Khokhar, the success of this shift, however, hinges upon the collaborative efforts of all the cement industry stakeholders. “Sustainable practices are no longer optional but essential. By exploring alternative fuels, investing in energy-efficient technology, and replacing clinker with other materials, the cement industry can curb its escalating emissions and work towards the crucial goal of net-zero emissions.”
Industry willingness
Luckily, the cement industry is cognisant of both the need for decarbonisation and the challenges involved in this shift. Many of the 26 cement producers have already started implementing solutions at different stages of the production process to reduce their carbon footprints.
The D.G. Khan Cement, for example, has reduced its carbon emissions by 14.6pc by reducing its coal use by switching to alternate fuels, renewable solar power and waste heat recovery technology, as well as reducing clinker usage.
“The industry can reduce its carbon footprint by minimising the use of coal, electricity and clinker. Although many companies in the industry have committed to decarbonisation, no individual player can achieve this goal without buy-in from across the ecosystem,” says Arif Bashir, DGK Cement director (technical & operations), as he narrates the story of his company’s efforts to cut carbon emissions through the cement value chain in the last few years to meet the demand for sustainably produced materials.
He says his company is developing a new Portland cement to reduce clinker use by 50pc. “Blended Portland cement replaces 50pc clinker with a blend of calcined clay and limestone. Studies are being conducted.”
He says the cement industry in Pakistan is actively exploring various strategies to reduce its CO2 emissions. “Ongoing adjustments in production processes and a transition from conventional fossil fuels to low-CO2 energy sources have already begun to facilitate a reduction in CO2 emissions.
“When combined with carbon capture, utilisation, and storage technologies, even more substantial emissions reductions will become feasible. There are opportunities to decarbonise the entire supply chain and reduce CO2 emissions in all cement manufacturing and distribution stages.”
Nonetheless, he argues, this net-zero emissions goal will be difficult to achieve unless international financing in the shape of cheap loans, grants and partnerships becomes available to the local cement producers as the cost of this transition can be formidably high.
Published in Dawn, The Business and Finance Weekly, July 15th, 2024
Dear visitor, the comments section is undergoing an overhaul and will return soon.